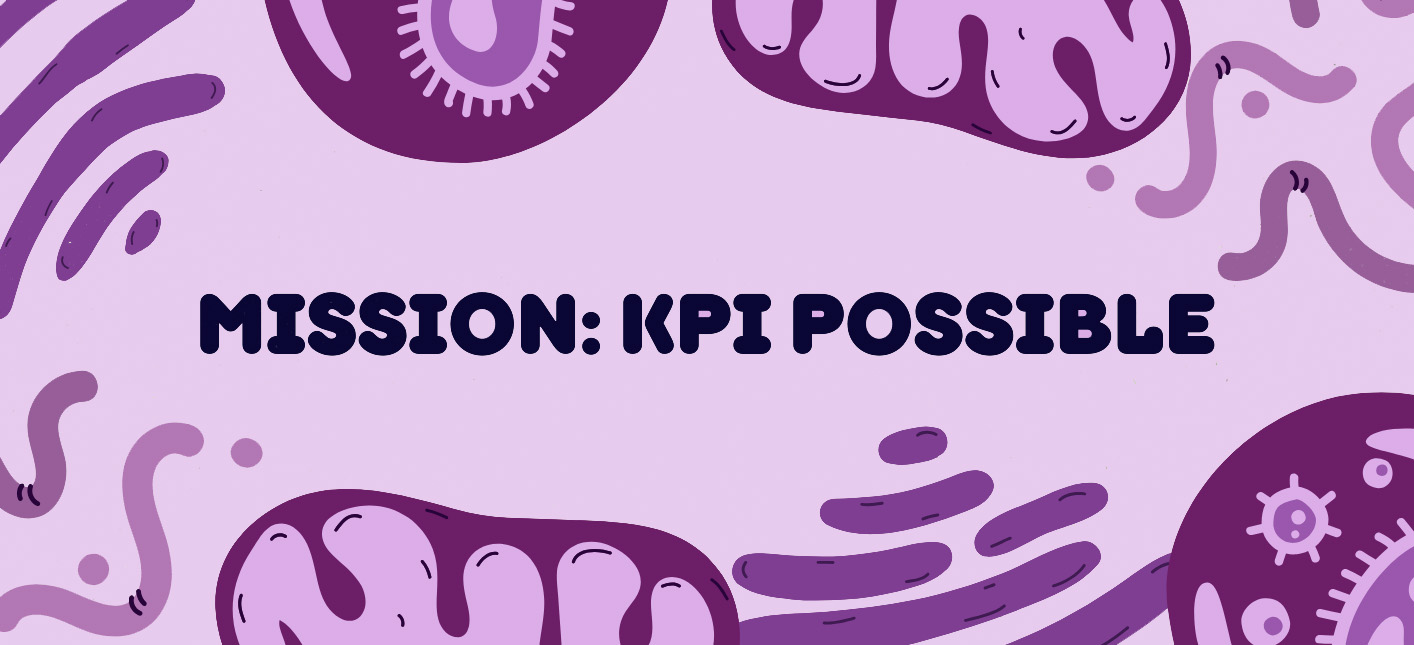
Mission KPI Possible
A journey towards GMP Compliance
In our continuous drive for operational excellence, we initiated an A3 called ‘Mission KPI Possible’. This A3 focused on increasing the completion rates of SUMMIT training modules for our operators. This initiative arose from the pressing need to address overdue trainings that led to red KPIs, indicating a lack of compliance with Good Manufacturing Practice (GMP) regulations.
“There was a notable lack of understanding”

KPI Leaderboard results
Identifying the core challenges
Using a Pareto chart, we began by identifying the core challenges that prevented operators from completing their SUMMIT training on time. Operators expressed that their day-to-day responsibilities, particularly performing assays and other critical tasks, took precedence over monitoring SUMMIT. There was a notable lack of understanding regarding the implications of incomplete trainings, which illustrated a behavioral issue. Operators also felt they did not have sufficient time to complete their SUMMIT, as well as feeling overwhelmed by the planning and the training backlog.
These responses indicated a significant opportunity to improve operators’ time management skills and find ways to alleviate their workload. Recognizing this, our KPI team embarked on an investigation, using ‘5 Why’, to delve into the root causes of this behavior.
Implementing targeted countermeasures
To address these insights, we implemented several targeted countermeasures aimed at boosting operator performance and accountability:
1.
Spotchecks
Conducted one-on-one sessions with operators stuck with pending trainings as well as random checks for those with SUMMIT items due within 14 days to reinforce accountability and the timeliness of training.
2.
Allocated time
We adjusted our daily planning schedule to include a specific 15-minute window each morning, dedicated exclusively to SUMMIT trainings. This approach ensured that operators had a focused period to complete their training items without interruptions from regular tasks. Spot checks during this time reinforced its importance.
3.
Weekly reminders
Every Monday, we shared a list of upcoming training sessions in our Tier 1 chat on Teams, highlighting the specific operators involved. This proactive communication helped operators plan their schedules, keeping training priorities visible.
4.
Leaderboard
To foster a culture of accountability and healthy competition, we established a leaderboard ranking operators based on their training progress. High-performing operators received recognition and rewards, such as small prizes for those ranked in the top three. Conversely, those in the last three positions faced light penalties, like bringing snacks for their team. This initiative encouraged proactiveness while promoting a sense of camaraderie among the team. The leaderboard is bustling with activity, and it’s great to see how each member contributes to our success.
Evaluating results
The outcomes of our A3 initiative have been promising! Since implementing these innovative countermeasures, we have observed a noticeable increase in the completion rates of SUMMIT trainings. Our operators are now more engaged and committed to their training responsibilities, with many reporting greater satisfaction and relief from the structured support provided. Moving forward, we will continue to refine our strategies and support our operators with their training. This initiative has not only improved KPI performance but has also cultivated a collaborative environment where operators feel empowered to take ownership of their learning!
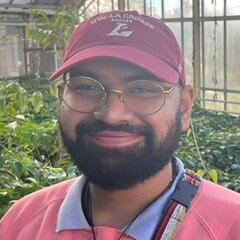
Zaki Lakhpatwala
Technician QC Microbiology (KPI team)
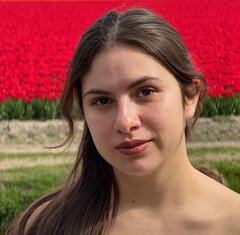
Shalom Martell
Technician QC Microbiology (KPI team)
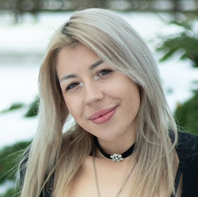
Rebeka Branda
Technician QC Microbiology (KPI team)
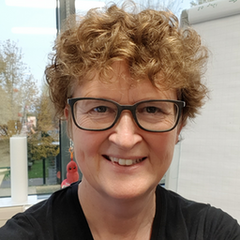
Clare Wildgoose
Supervisor QC Microbiology (coach A3)
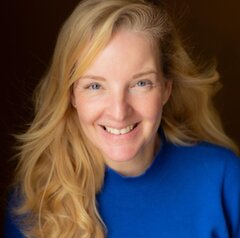
Suzanne Verhaegh
Manager QC Microbiology (Sponsor)
A3 training
An A3 is a lean tool used for problem solving and improvement processes within organizations. Although “A3” originally refers to a paper size, it is best known in lean contexts as a method of presenting information in a clear and concise manner.
It is a powerful tool that helps structure and clearly communicate information about problems and improvement actions.
For more information, also visit J&J's website, “JES EventDetails’, where J&J also offers training.
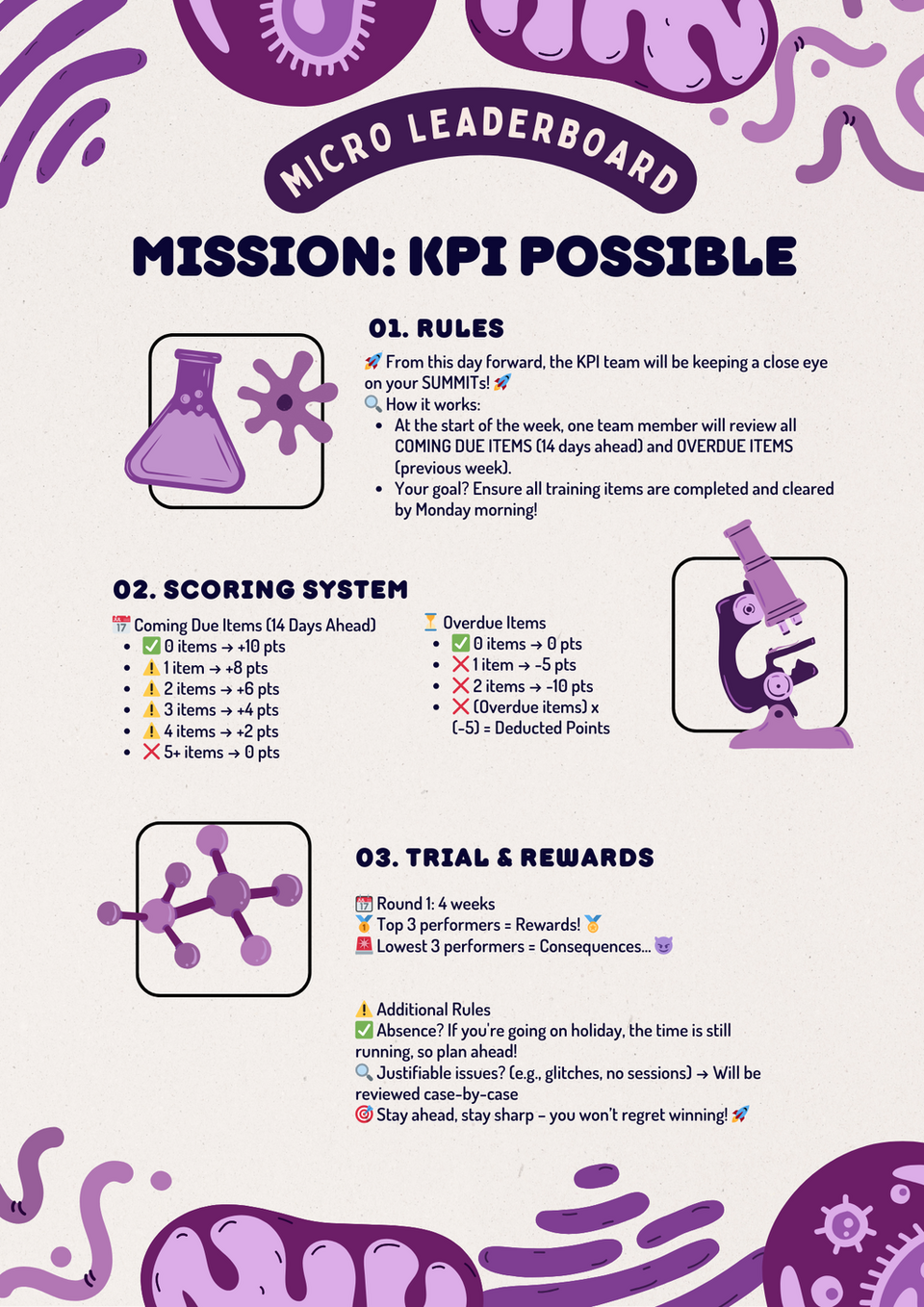
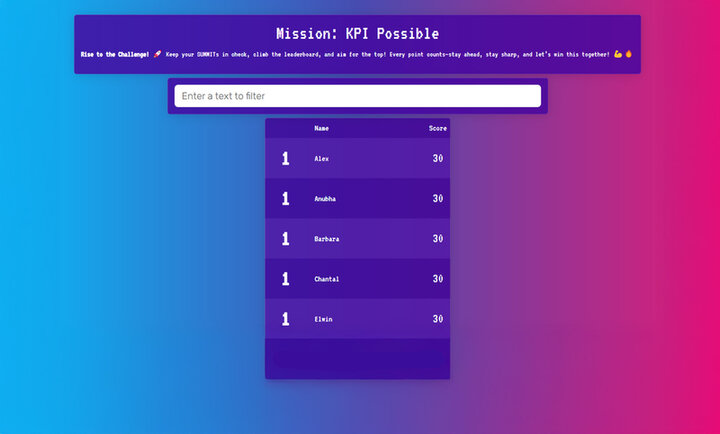
KPI Leaderboard results